Why it took me 2 years to release my first physical product
After almost exactly 2 years from the idea, to the first sketch to a finished product my custom designed coffee filter…
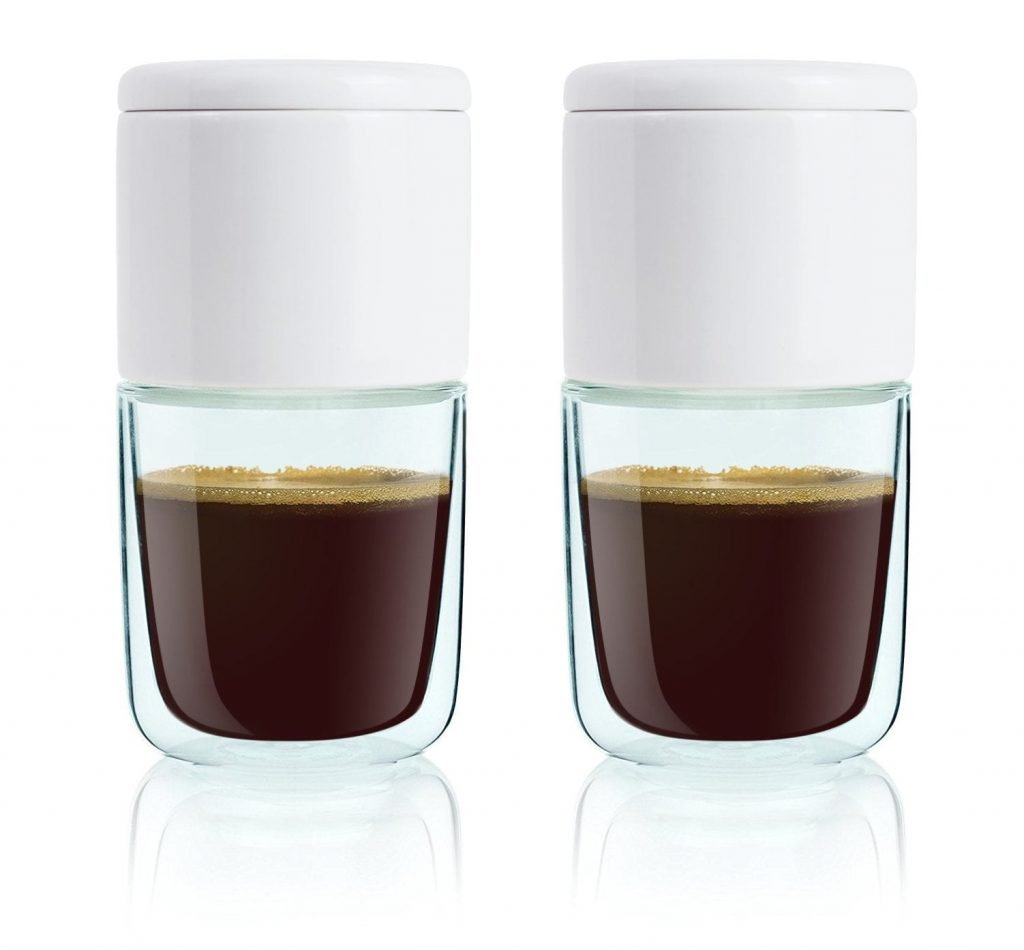
After almost exactly 2 years from the idea, to the first sketch to a finished product my custom designed coffee filter is finally ready to ship.
It’s been quite a long journey so far and I honestly didn’t expect it to take up so much time.
Looking back, my initial plan was to ship the product after about a year. But as always, things never work out as planned.
“Everyone has a plan ’till they got punched in the mouth.”
Mike Tyson
So why did it take me so lang to create a “simple” coffee filter?
Finding a good manufacturer takes time
You know, all designers want to make beautiful products. Spending a lot of time crafting the details and making every inch perfect.
Then we think we are done.
The bloody truth is, that design takes up such little percentage in the entire process of creating a product from scratch.
In my case, I spent around 2 – 3 months at the beginning to lay out the foundational concept.
Of course there was a bit more design work here and there, however, the majority of my time was really spent on finding a manufacturer.
Finding a manufacturer in general is easy, but finding the right manufacturer is damn difficult.
I talked to lots of manufactuers in Germany and China, sending concept drawings back and forth, getting quotes and ordering samples.
It took me more than 6 months to find a reliable manufacturer, who was willing to go through the process of refining the product with me.
The first sample is never right, also the second, and the third…
Creating a sample can still be a challenge even when you prototyped your product beforehand.
While 3D printing at the beginning helps to get a sense for the product, creating a sample with real material from a real manufacturer is another ballgame.
An expensive one as well.
You are restricted by the manufacturers capabilities and by the material limitations.
Every time I ordered a sample, I had to wait about a week for the money to be transferred, waiting another 4 weeks for the sample to be finished and then waiting another 2 weeks until it arrived at my doorstep.
Almost 2 months for a custom sample. And if the sample wasn’t working, I had to go through the whole procedure again. That happened multiple times because each time there was another detail that didn’t work out.
Changing designs in the middle
Because my product consists of different materials, I also had to talk to manufacturers in multiple categories and managing logistics between them. This took up a lot of time and monetary investment as well.
I could have been smarter about this from the beginning.
The sample making process also revealed design flaws that I haven’t spotted before.
Due to the lack of air vents, the hot water created a pressure that led the coffee to spill outside the glass.
Those kind of things you can only spot when testing with real materials under real conditions.
This required me to redesign the entire bottom of the filter and ditch the filter paper method. Consequently, I had to look for another manufacturer, again.
Logistics as the top of the ice berg
When the sample was finally done, it was ready for mass manufacturing.
Creating a single sample and making it perfect is difficult enough, but when it comes to mass manufacturing, you have to consider tolerances.
Even when products come from the same production line, you will never have exactly the same products.
Especially when dealing with multiple manufacturers the factor for failure grows exponentially.
Suddenly, glasses didn’t match with the ceramic, things got broken during the transport from one place to the other and the delay of one manufactuer can cause a delay for the others.
Shipping products across the world during christmas time is also a big challenge. Manufactures are running at max and logistics company are fully booked. It took almost 1 months for the products to arrive at the amazon warehouses per air express!
(in an ideal case, this shouldn’t take much more than 2 weeks).
Life events got in the way
Besides all the challenges of creating a product from scratch, I also had to manage my personal life and my full time job.
Last year, I had multiple opportunites to travel for work which set back my project for a couple of months.
I also left my full time position at frog in february which caused another slight delay in my timeline.
As you see, there lots of challenges that come along with creating your own product but the satisfaction of holding something in your hands that is 100% yours makes up for all the hurdles you have to take.
I had a lot of moments where I wanted to quit, so I guess the most important lesson here is to keep going no matter what. Because until it’s not out in the market, you will never know if it’s a success or not.
Nevertheless, I had a lot of learnings along the way and and there is much more to come.
But now it’s time to hustle and develop yet another important skill: Sales.